Pellet Extruders
RD-M40NEXT-GEN PELLET EXTRUDER
The RD-M40 is a next-generation high-flow and medium weight pellet extruder. It was designed to 3D print components as fast and cost-effective as possible. It can be combined with robots or CNC machines. RD-M40 is able to output up to 40kg of material per hour.
Available for order
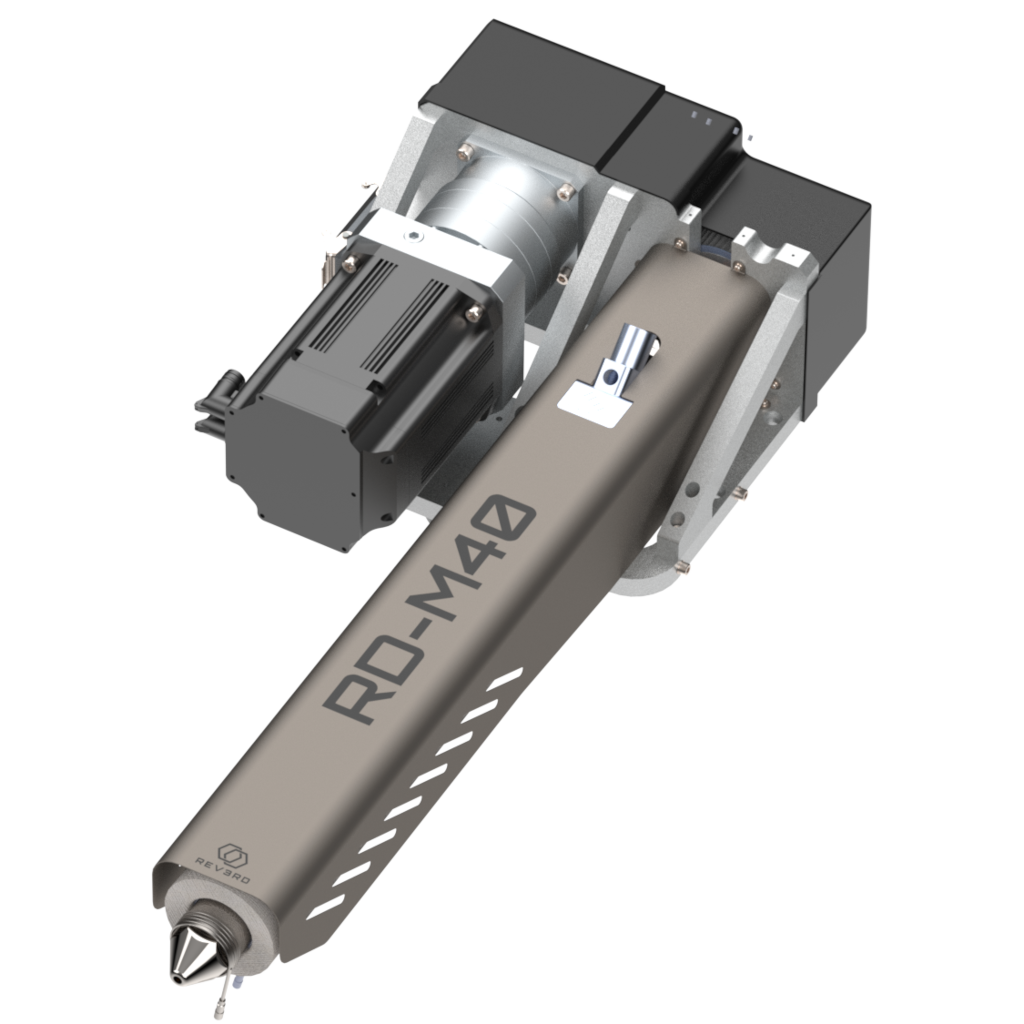
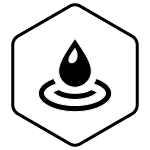
Water Cooling - Hot Environment Ready
The RD-M40 is able to operate in any environmental condition. The water-cooling loop keeps the whole system (motor, screw shank, reducer and feeding zone) at a constant temperature.
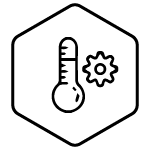
4 Zone Heating Barrel Control
The quadruple heat zone design helps to keep the polymer at a constant temperature. The feeding section receives cold pellets and generates more heat to melt them. Then, the compression zone stabilizes the polymer at a precise temperature ensuring the plastification process (all the solid pellets turn into a molten status). Finally, the metering heater ensures an even flow.
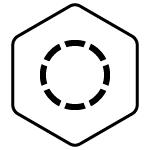
Multiple Nozzle Size
RD-M40 can be used with large nozzles from 3.00mm up to 12.00mm. They can also be customized.

Customized Extrusion Screw
The bimetallic customized screw design is optimized for high-resolution 3D printing. Two tapered bearings, which support the screw, allow a low friction rotation, a bore centering of the screw in the barrel and can handle the whole high axial force required to extrude in high-speed and pressure conditions.
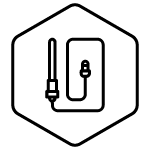
Melting Zone Sensor
The temperature sensors are placed only 0,5 mm away from the molten polymer. Readings are reliable and accurate.
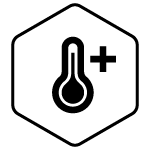
Precise Temperature Control
The four K-type thermocouple sensors are class 1, high precision sensors. The circuit has been designed to use the best resolution between 20°C and 500°C.
Powerful SERVO Motor
The powerful Geared SERVO MOTOR can handle high flow without any strain. To maximize RD-M40 extruder’s compatibility, the motor driver can accept step and direction signals, 0-10V, EtherCAT, CANopen or RS-485 as communication protocols.
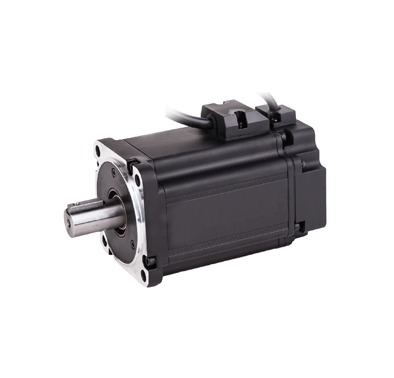
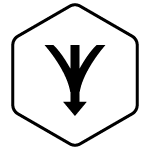
Breaker
The fast speed of RD-M40 is managed by a breaker. Like the faucet filter does with the water, the breaker aligns the output flow in order to avoid the spiral effect created by high-speed.
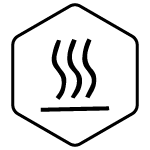
Uniform Heating
The spiral heaters wrap the whole heated barrel and ensure uniform temperature along the whole length end of the extruder.
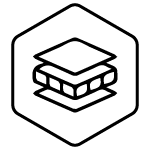
Insulation Blanket
A special insulation blanket is used to coat the Cylinder, in order to keep the heat inside and save the energy required to reach the temperature setpoints.
Automatic Feeding System
RD-M40 can come with an optional venturi feeding system which detects the pellets level and auto-charges the extruder. Pellets can be delivered from a bulk source or directly from a dryer.
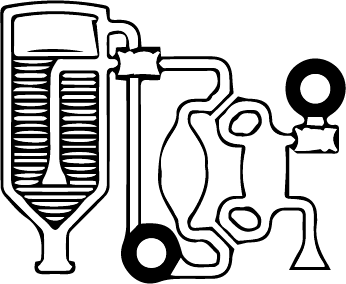
Dryer
This system is necessary to remove moisture and avoid faulty parts when printing hygroscopic compounds. RD-M40 can come with different dryer capacity: 12, 25 or 50 kg per hour.
Technical Specifications
RD-M40
PARAMETER | VALUE |
Weight | ~90 kg |
Screw diameter | 40 mm |
Max temperature | 500 °C |
Max environment temperature | 100 °C |
Available nozzle sizes | from 2.0 to 20.0 mm |
Max flow | up to 50 kg/h |
Total lenght | ~1150 mm |
Screw lenght | 20D |
Heating power | 5000 W |
Compression ratio | 2.5 |
Cooling | water cooled |
Power servo motor | 5-7.5 kW |
Planetary gearbox ratio | from 5 to 20 |
Belt trasmission ratio | from 0.5 to 2 |
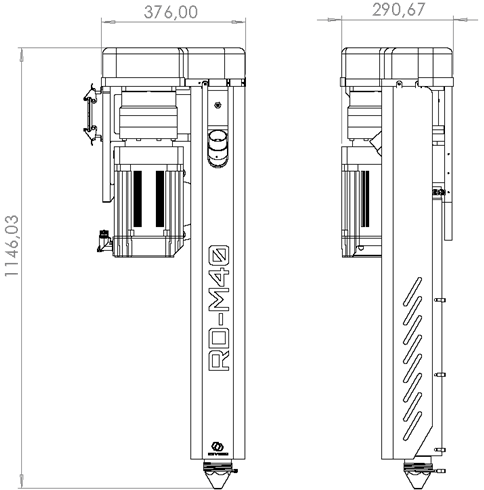